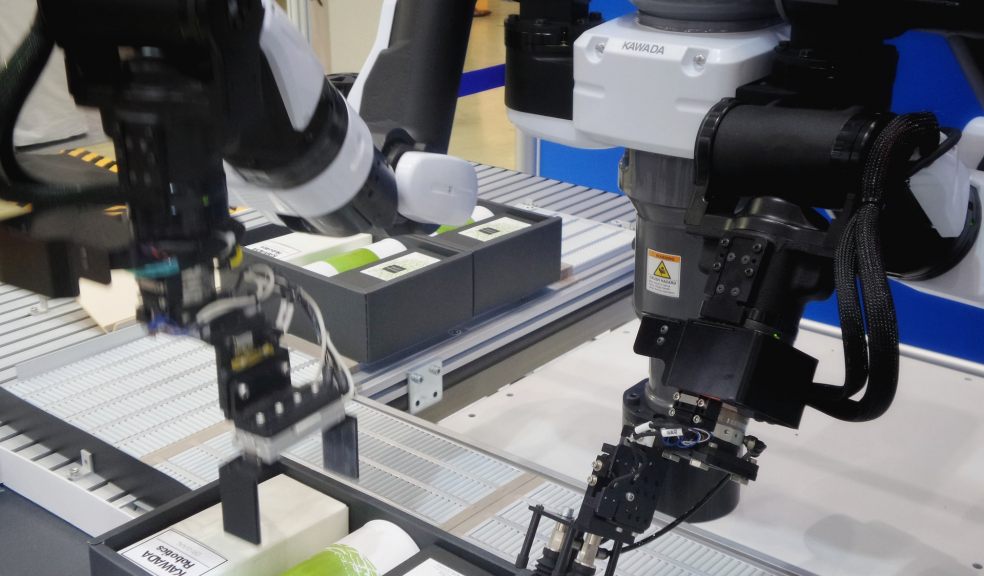
The benefits of using packaging robots
Material handling robots make packaging applications easy. The Universal Robots are fitted with collaborative technology for automated bin picking ana packaging. The collaborative arms can perform different tasks in a production plant with precision.
Packaging, palletizing, bin picking and kitting applications make the processes easy to handle. The following are the benefits of using packaging robots.
Reprieve for Worker
Some tasks in an industrial plant involve a lot of repetition, which can reduce the workers' motivation. Packaging robots perform these tasks instead of engaging humans. The robots never get tired, and they perform the same task over and over with precision. Other tasks involve heavy lifting, which can cause injuries to the workers.
Injuries among the workers can be avoided by using the automated collaborative arms to do the heavy lifting. Relieving workers from dull and dangerous jobs should be the ultimate goal for the production industries.
The Robots Can Be Used For Multiple Tasks
The cobots are fitted with artificial intelligence, which can pick a wide range of objects. The packaging robots can pick up products of any size and shape which makes the warehousing, logistics, and supply chain operations easy, faster, and more efficient. The automated packaging robots save the time that could have been wasted when shifting workers from one task to another.
Reduces the Cost Of Production
Automation shortens the product life cycle and reduces the cost of producing new products. During high peaks, most companies experience a shortage of labor due to production demands. Using automated packaging robots can combat labor shortages because they work faster than humans. The robotic machines constantly work without taking any breaks, thus increases production.
The robotic arms do not come with additional costs associated with traditional robots. You can maximize the robotic automation by engaging it to do numerous tasks without incurring extra costs.
Easy To Program
The packaging robots have an easy-to-program interface suitable for small-volume applications and also highly repetitive tasks. Repeating a task several times can be boring and may lead to a lack of concentration, which can result in errors. The packing robot can be programmed and redeployed to suit your workflow due to their small size and lightweight. Universal Robots are flexible, unlike the big robots, which may prove difficult to reprogram.
Saves On Space
The UR robots are small in size and thus save on the space. The robot arms of the Universal Robots can be disintegrated to free up a workspace to enable you to tackle important tasks. Due to their small size, the robots can be hanged on the walls or placed under the tables to create more working spaces. These robotic machines can be easily reprogrammed and be used with many different machines.
Increases Production
During peak seasons, when production volume is high, the Universal Robots can work 24/7. The cobots can deliver non-stop productivity as long as there is a steady supply of materials. Universal Robots can be redeployed, reprogrammed to do different tasks for as many times as needed. During busy seasons, a lot of packaging is needed, which cannot be handled by humans. Robots never take breaks. Neither do they get fatigued; thus, they will produce high volumes as required.
They Are Cost-Effective and Easy To Deploy
The use of collaborative robots saves on the money that could have been used to pay for wages. Besides getting salaries every month, humans require insurance and medical bills to cover them when they get injured. The companies also incur direct and indirect costs when the workers miss workdays due to injuries or illnesses. Universal Robots never ask for wages or insurance. The robots also work throughout without asking for leaves, and thus they use less money compared to humans.