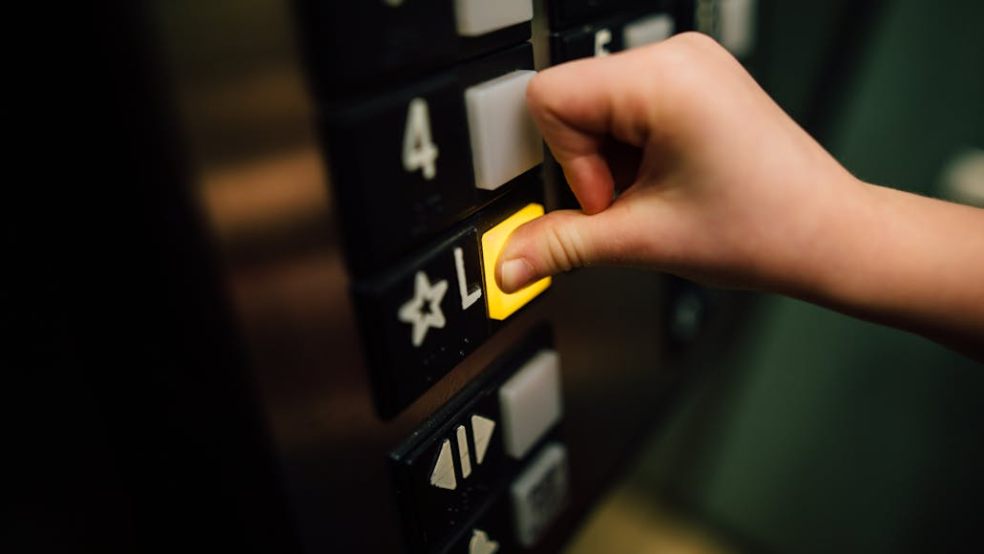
The Impact of Goods Lifts on Reducing Workplace Injuries
The Health and Safety at Work Act 1974 was brought in to place a duty on employers to take reasonable steps to minimise the risk of manual handling accidents. Despite this, there have been many incidents over the years of workers becoming injured through incorrect handling techniques.
Goods lifts reduce the chances of workers becoming injured by minimising the risks associated with manual handling and other hazardous workplace activities. A bespoke goods lift, engineered to meet specified requirements, uses cutting edge technology to optimise handling processes in the safest way.
Prevention of slips, trips and falls
The UK’s Manual Handling Operations Regulations 1992, which all employers must comply with, place emphasis on minimising manual handling as much as possible to reduce the risk of injury. Manual handling is defined as the movement of goods by lifting, pulling or pushing. Any one of these can easily cause injuries, which could have long-term implications for employees and employers.
A goods lift eliminates the need for employees to lift or carry heavy loads. By automating the movement of goods, a lift can help to prevent musculoskeletal disorders as well as trips, falls and the risk of goods falling onto a person. These are the most common types of manual handling injury, often caused by repetitive strain or lifting heavy goods beyond a worker’s ability.
A goods lift allows goods to be transported securely between levels, reducing the likelihood of items being dropped or workers tripping and falling while carrying heavy loads on stairs.
The enhancement of load stability for safety
Goods which may be of an odd shape or uneven weight can be difficult to pick up and can often cause a worker to lose their grip and drop the goods. This can in turn lead to injuries and costs to the business of replacing broken goods.
Lifts provide a stable and enclosed platform for goods to minimise the risk of items shifting or falling while in transit. And with bespoke ergonomic design, workers can load and unload goods at optimal heights. Doing so reduces them having to adopt an awkward or unsafe posture, which can lead to muscular injuries.
Increase efficiency by reducing fatigue
Carrying heavy loads manually throughout the working day can be extremely tiring. A fatigued worker is more likely to make mistakes or injure themselves and potentially need to take time off work.
This can be avoided by using a mechanised automated goods lift to move heavy items between floors. This helps greatly in lowering the risk of injuries and errors caused by fatigue or inattention and helps to improve efficiency and productivity.
Supports compliance with UK workplace standards
Installing a goods lift will help businesses to meet their legal obligations under the Health and Safety at Work Act 1974, which places the responsibility for providing a safe working environment free from hazards squarely onto employers. They should also provide any training necessary but must also carry out regular risk assessments and provide equipment to enable workers to do their job safely.
If a worker becomes injured through unsafe manual lifting procedures this could lead to significant downtime for the employee. It could also lead to downtime for the business if they have to suspend operations. If failure to comply with safety regulations is proven by HSE inspectors, there could be significant costs or even legal proceedings.
Through the installation of a goods lift, businesses can create a safer workplace and improve productivity as workers are less likely to be injured. A bespoke goods lift allows the seamless transportation of goods between floors, reduces the risks of manual handling injuries and provides safe access to all areas of the workplace.