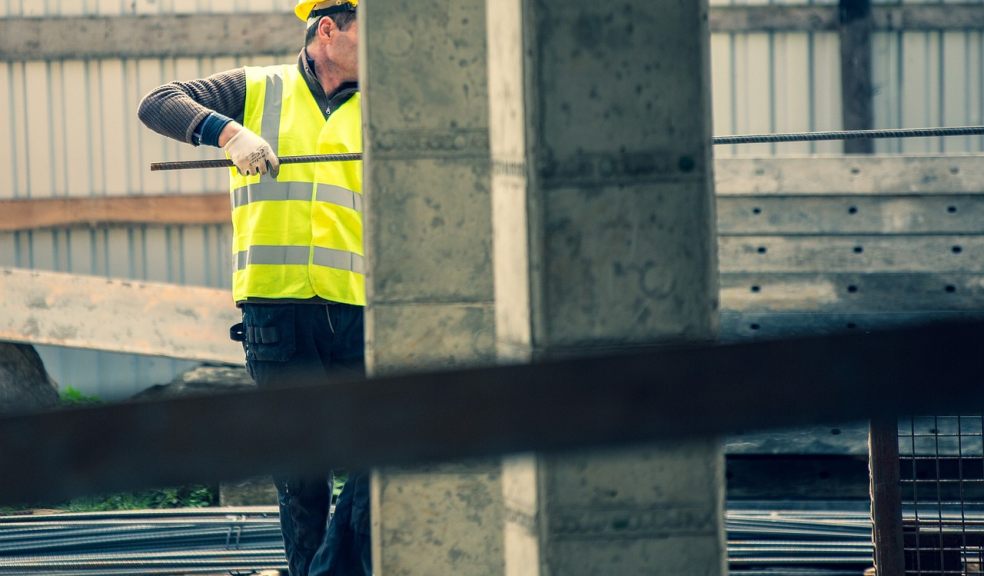
Key Applications of Ultrasonic Scanners in Industrial Inspections
Industrial inspections depend heavily on ultrasonic scanners because they deliver non-destructive testing (NDT) solutions for material and structural integrity assessment. Industry scanners use high-frequency sound waves as their detection method to examine internal defects while measuring thickness and testing material properties with superior precision. Ultrasonic scanners prove essential in industry operations because they provide immediate results without any damage to materials. The ultrasonic scanner serves key functions in aerospace industries while supporting automotive sectors and oil and gas applications and power generation companies and construction sites. This paper explains how ultrasonic scanners are used in industrial inspections through their essential functions for quality maintenance and safety and operational efficiency.
Ultrasonic Scanners For Weld Inspection
Multiple industrial sectors like aerospace manufacturing together with oil and gas depend on welded joints as critical elements. The safety performance standards rely on maintaining the integrity of welds since they form a foundation for structural integrity. Ultrasonic scanners serve an essential function to identify weld defects that include cracks together with voids and porosity which weaken weld structures.
How Ultrasonic Testing Works in Weld Inspections
UT technology applies high-frequency sound wave transmissions toward weld examination. High-frequency sound waves transmit through the weld to encounter discontinuities where some waves reflect to the transducer so technicians can interpret the signals to detect anomalies.
Advantages of Ultrasonic Scanners in Weld Inspection
- UT tests deliver extremely precise measurements which allow the detection of smallest material flaws.
- The ultrasonic scanners provide exceptional penetration ability to expose both hidden and visible structural defects deep inside the material.
- The testing method employs non-destructive techniques since it preserves testing objects from damage.
- These devices enable inspection of different weld varieties alongside several material types including metallic components and alloys.
Industries Where Weld Inspections Are Critical
- Weld inspections for pipelines and offshore structures in the oil and gas industry need strict procedures because catastrophic failures would occur otherwise.
- Aerospace aircraft components need to pass defect testing to assure safety in flight operations.
- The manufacturing sector needs welded components to pass through strict quality requirements across heavy machinery and infrastructure building applications.
Challenges in Weld Inspections and How Ultrasonic Scanners Help Overcome Them
- Welds with irregular shapes challenge inspectors because they create obstacles for inspection work. Advanced NDT scanners possess the capability to scan weld shapes of diverse configurations.
- The interpretation of results depends on expert technicians although automated UT systems achieve better consistency and accuracy.
- The signal transmission in modern UT equipment features adaptive technology that addresses surface conditions which include rough or painted surfaces.
Using Ultrasonic Scanners For Corrosion Assessment
The industries of oil and gas and marine and power generation experience considerable deterioration through the process of corrosion. Time exposes materials to corrosion until they reach points where leaks and structural failures become likely while necessitating expensive repaire. The usage of ultrasonic scanners allows an efficient way to detect corrosion levels within key infrastructure systems.
Benefits of Ultrasonic Technology in Corrosion Evaluation
- The accurate thickness readings from UT enable the discovery of corrosion at its early stages.
- The technique detects pitting and erosion conditions that exist outside external viewing range.
- Early detection through this method enables industry stakeholders to perform preventive maintenance which decreases failure risks.
Corrosion Mapping and Automated Scanning Systems
The process of corrosion mapping requires comprehensive scanning to build detailed representations that show material thickness levels. The process obtains enhancement through automated ultrasonic scanners.
- The automatic systems deliver fast scanning of extensive material surfaces.
- Sustainable automated scanning procedures decrease occurrences of human mistakes throughout inspection processes.
- Advanced UT systems create detailed maps from scanned data to enhance future analysis and decision-making.
Long-Term Advantages of Ultrasonic Scanners for Corrosion Monitoring
- The system helps identify material thinning together with defects before they reach critical stages.
- The inspection system produces cost savings by helping operators prevent maintenance failures before they happen in addition to allowing proactive maintenance approaches.
- The monitoring system enables a longer operation span for assets which results in decreased needs for premature technical replacements.
- The examination techniques avoid destructive testing methods to inspect material conditions without harming the tested component.
- The system maintains safety levels by ensuring the reliability of crucial infrastructure which decreases the potential for dangerous accidents.
- Accurate and Consistent Data – Provides precise measurements for long-term condition tracking.
- The inspection process becomes more efficient and fast because it reduces operational delays while maintaining uptime.
Ultrasonic Scanners for Inspecting Composite Surfaces
Accurate non-destructive defect identification of composite surfaces depends on ultrasonic scanners. They identify delaminations voids and cracks. Multiple layers of composite materials can be evaluated through these scanners while the inspections happen without causing damages to the materials. The superior imaging features of their system ensure both structural safety and product quality improvement alongside greater reliability of composite materials for multiple industrial applications.
The operation of ultrasonic scanners for examining composite materials
Sporting goods companies use ultrasonic scanners to inspect composite structures by emitting sound waves which generate reflected data used for detecting hidden flaws within the material. UT possesses the capability to detect defects inside composite materials which qualifies it as an essential instrument for quality evaluation.
Key Advantages of Ultrasonic Testing for Composites
The ultrasound testing method provides essential advantages when inspecting composite materials.
- The ultrasonic waves enable detection of flaws that lie beneath multiple composite layers.
- The testing method requires no material alteration or damage for inspection procedures.
- Ultrasonic technology provides two essential benefits which ensure composite parts maintain their required safety and performance standards.
Practical Uses in Aerospace and Automotive Industries
- Ultrasonic scanners operate in aerospace component inspections to identify defects within aircraft fuselages along with wings and vital composite structures thereby guaranteeing safety performance.
- These scanners provide automotive companies two key tests through material thickness evaluation alongside weld integrity verification to improve both performance and durability.
Key Benefits of Ultrasonic Scanners in Industrial Inspections
Some key advantages of ultrasonic scanners exist in various industrial applications. Ultrasonic scanners offer essential non-destructive evaluations that make them vital for the purpose of safety assurance and reliability enhancement and regulatory compliance.
- Non-Destructive Testing (NDT) serves to inspect materials and structures by creating no destruction to them.
- High Precision and Accuracy – Detects even the smallest defects with reliable measurement data.
- The inspection process becomes faster and more effective through ultrasonic scanners thus reducing operational delays.
- Versatility Across Materials – Works on metals, composites, and other industrial materials.
- The enhancement of safety alongside quality control measures occurs through this method which preserves structural integrity.
Conclusion
Through ultrasonic scanners the industrial sector has experienced a revolution in inspections which delivers exact assessments without structural damage of welds corrosion and composite materials. Entrepreneurs around the world choose ultrasonic scanners because they play an essential part in preserving infrastructure reliability and creating safer environments at a lower maintenance cost. Ultrasonic inspection methods will become more advanced through technology development to produce better industrial quality control and safety assurance systems.