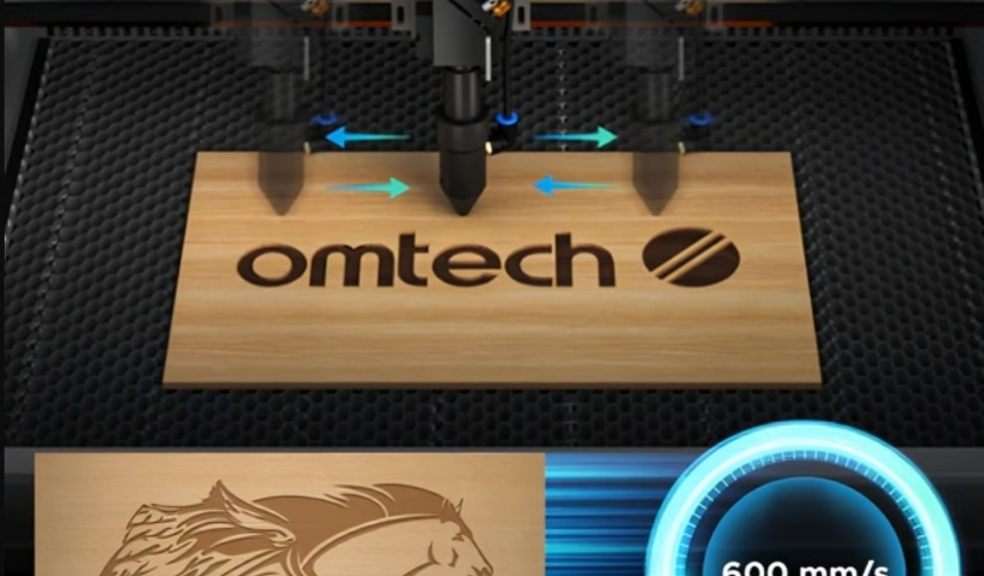
Exploring the Science Behind Laser Cutting Technology
Laser cutting technology has revolutionized manufacturing and design, offering precision and efficiency unmatched by traditional methods. Among the remarkable machines in this domain, the OMTech 50W CO₂ laser cutter stands out, delivering high performance and versatility for professionals and hobbyists alike. This article delves into the science behind laser cutting and explores how this innovative technology works.
Understanding Laser Cutting Technology
A. Definition and Basic Principles
Laser cutting involves using a focused beam of light to cut or engrave materials with exceptional precision. CO₂ lasers, in particular, are widely used due to their ability to cut a variety of materials, such as wood, acrylic, and plastics, with minimal waste and high accuracy.
B. Historical Development
Developed in the 1960s, laser cutting has evolved significantly over the decades. What began as a tool for industrial applications has become an indispensable technology across industries, from manufacturing to the arts.
The Science Behind Laser Cutting
A. Laser Generation and Amplification
CO₂ laser cutters generate beams by exciting a mixture of carbon dioxide, nitrogen, and helium gases with an electrical current. This process produces a powerful beam of infrared light that is focused and amplified for cutting or engraving.
B. Interaction with Materials
When the laser beam contacts a material, the concentrated energy rapidly heats the surface, causing it to melt, vaporize, or burn. This precision minimizes material waste and allows for intricate designs.
C. Precision and Control
The precision of laser cutting is achieved through advanced control systems. Factors such as beam intensity, focus, and speed are meticulously calibrated to ensure clean and accurate cuts.
Components of a CO₂ Laser Cutting System
A. Laser Source
The OMTech 50W CO₂ laser cutter uses a CO₂ laser tube, which provides consistent power and efficiency for cutting and engraving tasks.
B. Motion Control System
The CNC system precisely guides the laser beam along the desired cutting path, enabling the creation of complex designs with minimal error.
C. Optics and Focusing Mechanism
Mirrors and lenses within the system focus the laser beam onto the material, ensuring optimal energy delivery and sharp cuts.
D. Cooling and Ventilation
Efficient cooling systems, such as water chillers, and proper ventilation are critical to maintaining consistent performance and safety during operation.
Applications of Laser Cutting Technology
A. Material Versatility
Laser cutting is highly versatile, capable of processing materials like wood, acrylic, plastics, fabric, and thin metals. This adaptability makes it ideal for a variety of projects.
B. Industry Use Cases
Industries such as automotive, aerospace, architecture, and fine arts rely on laser cutting for precision manufacturing and creative endeavors.
Considerations When Using Laser Cutting Technology
A. Material Preparation
Properly preparing materials, such as cleaning surfaces and securing them in place, enhances cutting quality and consistency.
B. Maintenance and Care
Routine maintenance, including cleaning lenses and checking the laser tube, is essential for prolonging the machine’s lifespan and maintaining its performance.
C. Safety Protocols
Following safety guidelines, such as wearing protective eyewear and ensuring proper ventilation, minimizes risks associated with laser operation.
Conclusion
Laser cutting technology represents a fusion of science and practicality, transforming industries with its precision and versatility. Machines like the OMTech 50W CO₂ laser cutter are at the forefront of this transformation, enabling creators and manufacturers to achieve extraordinary results. As we look to the future, the possibilities for laser cutting are boundless, promising even greater contributions to innovation and design.