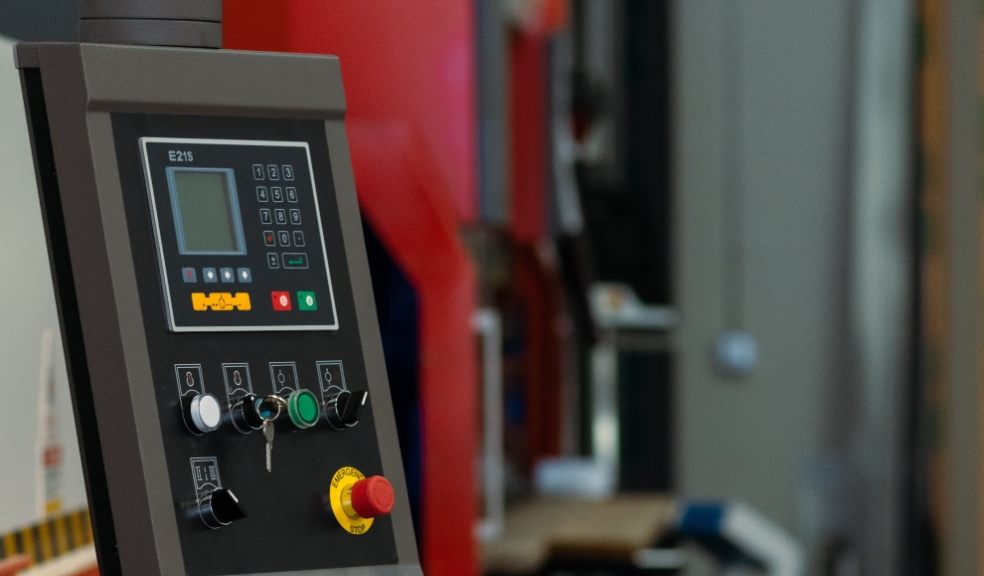
Optimizing Injection Moulding with Structural Foam
Let's dive into the exciting world of structural foam! In this article, we will explore the latest improvements in the product, comparing it to traditional injection moulding techniques. We'll also take a closer look at the materials and additives used in structural foam. So, let's get started and discover the incredible advancements in injection moulding large plastic products using this foam!
Enhanced Strength and Durability in Structural Foam
Structural foam has experienced remarkable advancements in terms of strength and durability. Unlike traditional injection moulding, which relies on solid plastic, structural utilizes a cellular core structure. The inclusion of a foaming agent during the moulding process creates a lightweight yet sturdy internal structure. This innovative approach results in products that are stronger and more resistant to impact and stress.
It offers exceptional load-bearing capabilities, making it ideal for manufacturing large plastic products such as automotive parts, furniture, and even recreational equipment. The cellular structure provides excellent dimensional stability, ensuring that the final products maintain their shape and structural integrity over time.
Structural Foam vs. Traditional Injection moulding
When comparing structural foam to traditional injection moulding, the advantages become evident. Traditional relies on solid plastic, which can be costly and time-consuming. On the other hand, Structural offers cost-efficiency due to reduced material usage and shorter cycle times.
Moreover, its cellular core structure provides improved insulation properties, making it an excellent choice for products that require thermal resistance. The foam interior also allows for more design flexibility, enabling the integration of complex shapes and features that would be challenging to achieve with injection moulding.
Structural Foam Materials and Additives:
To achieve the desired properties and performance, structural foam utilizes various materials and additives. The base materials used can include polyethylene, polypropylene, polystyrene, and even engineering-grade resins like ABS or PC/ABS blends. These materials offer a wide range of physical and mechanical characteristics, allowing manufacturers to tailor the foam to specific application requirements.
Furthermore, the addition of additives enhances the foam's properties. Reinforcing agents such as glass fibers or mineral fillers can be incorporated to increase strength and rigidity. Flame retardants ensure compliance with safety regulations, while impact modifiers improve resistance to external forces. By carefully selecting the materials and additives, manufacturers can customize the structural foam to meet the unique needs of each application.
In conclusion, structural foam has undergone significant improvements in recent years, revolutionizing the moulding industry. Its enhanced strength, durability, and cost-efficiency make it a preferred choice for manufacturing large plastic products. The cellular core structure, along with a variety of materials and additives, allows for exceptional design flexibility and tailored performance.
As the demand for high-quality plastic products continues to grow, it proves to be a game-changer. Whether it's for automotive parts, furniture, or any other application requiring strength and durability, structural foam moulding offers a reliable and cost-effective solution.