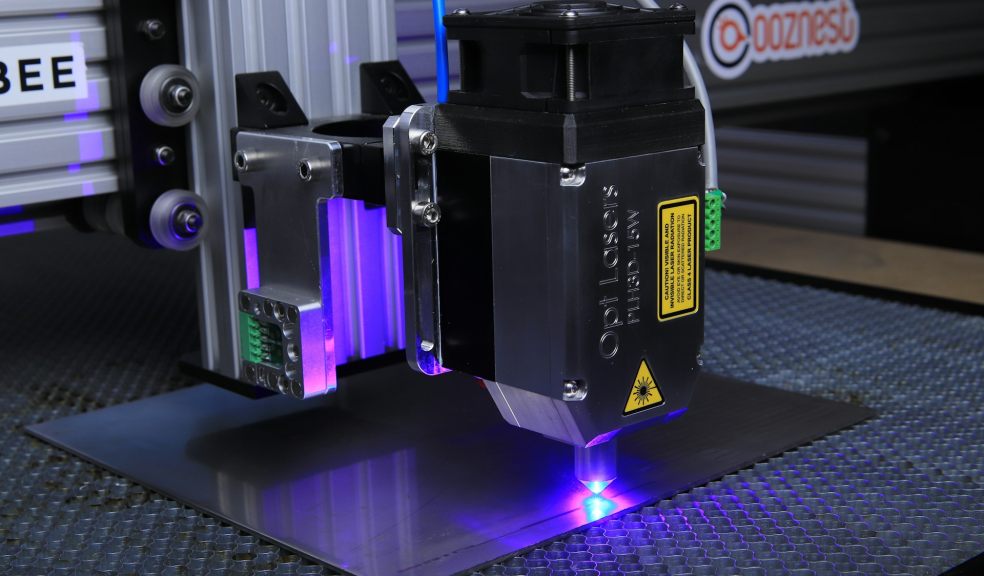
The Future of Fabrication: Laser vs. Traditional Cutting Techniques
Selecting the right method to cut materials can greatly affect everything, from the quality and cost of your final product to how quickly you can make it. Laser cutting has become very popular because it's precise and can handle many different tasks.
Interestingly, a laser strong enough (12 kW with oxygen assist) can cut through a 40-mm-thick steel sheet ten times faster than a bandsaw and 50 to 100 times faster than wire cutting. This highlights the advantages of having your metal parts laser cut over traditional cutting methods. Let's explore how laser cutting compares to traditional methods of cutting.
What is Laser Cutting?
Laser cutting uses a concentrated laser beam to cut through materials such as metal, plastic, and wood. This method is precise and efficient, making it great for cutting out complex shapes and fine details without wasting much material.
Compared to traditional cutting methods, which often involve physical contact between a tool and the material, the non-contact nature of a laser cut reduces wear and tear on tools and can minimise the damage to the material being cut.
Laser cutting Vs. Mechanical Cutting
Mechanical cutting, which includes the use of saws, shears, and routers, relies on physical tools to make cuts. These tools physically touch the material, which can sometimes lead to inaccuracies or damage to both the tool and the material.
Mechanical cutting is effective for straightforward, less intricate tasks but often struggles with more complex designs. Laser cutting, on the other hand, allows for a higher level of detail and maintains consistent precision, regardless of the complexity of the pattern.
Laser Cut vs. Water Jet Cutting
Water jet cutting uses high-pressure water, sometimes mixed with an abrasive material, to cut through hard substances like metal and stone. This makes it extremely powerful, allowing it to cut through thick materials without generating heat, which prevents the material properties from changing due to temperature.
However, water jet cutters are generally slower and more expensive to operate than lasers, as they consume a lot of water and abrasive materials.
Laser Cut vs. Plasma Cutting
Plasma cutting is a traditional method mainly used for cutting materials that conduct electricity, like copper, stainless steel, and aluminium. It works by sending an electric spark through a gas that flows through a narrow space, turning the gas into plasma. This plasma is hot enough to cut through the material.
While plasma cutting is faster than some older methods for cutting thicker materials, it does not match the precision of laser cutting. However, plasma cutting works quite well for plates that are around 50 mm in thickness. The upper limit is plates of up to 150 mm thickness, which is much higher than what laser cutting can handle. The heat generated by plasma cutting can also affect the integrity of the material around the cut, known as the heat-affected zone (HAZ), potentially leading to material warping or other distortions. While laser cutting also creates HAZ, it is less than what occurs with plasma cutting.
With the introduction of more powerful lasers, laser cutting is eating into plasma cutting territory, but it is still widely used for thicker plates. Additionally, not all manufacturers have the latest and most powerful laser cutters because of their hefty price tags.
Benefits of Choosing Laser Cutting
While there are many pros and cons of laser cutting, here are the major pros of using laser cutting technology:
Precision and Quality
Precision is one of the main advantages of laser cutting. The laser beam can be focused to a pinpoint, allowing for intricate details and clean cuts. This level of accuracy ensures high-quality finishes without the need for additional processing.
Speed and Efficiency
Laser cutting is significantly faster than most traditional methods when it comes to processing large batches of material. This speed translates into lower production times and costs, making laser cutting a cost-effective choice for both high-volume production and custom projects.
Versatility
Lasers can cut a variety of materials and thicknesses, which makes them incredibly versatile. With such flexibility, manufacturers can use laser cutting for multiple projects without needing to change tools or set up new equipment for different materials.
Reduced Damage and Safety
Since laser cutting does not require direct contact with the material, there is less risk of mechanical damage to the material being cut. Also, the non-contact nature of the process means there is a lesser chance of accidents compared to traditional cutting methods.
Environmental Impact
Laser cutters are more energy-efficient and produce less waste than traditional cutting methods. They do not require the use of water or abrasives and generally have a smaller footprint in terms of waste management and disposal.
Wrapping Up
Laser cutting clearly emerges as a better and superior option when compared to other cutting methods because of its unmatched precision, fast operation, and flexibility. The technique is also safer, creates less waste, and can handle many different types of materials and thicknesses with comfortable ease.
If you're thinking about how to make your production more effective and precise, laser cutting might just be the smart move that can take your business forward.